Electrical vehicle new era - High Voltage Wire Harness Design
2024.05.15
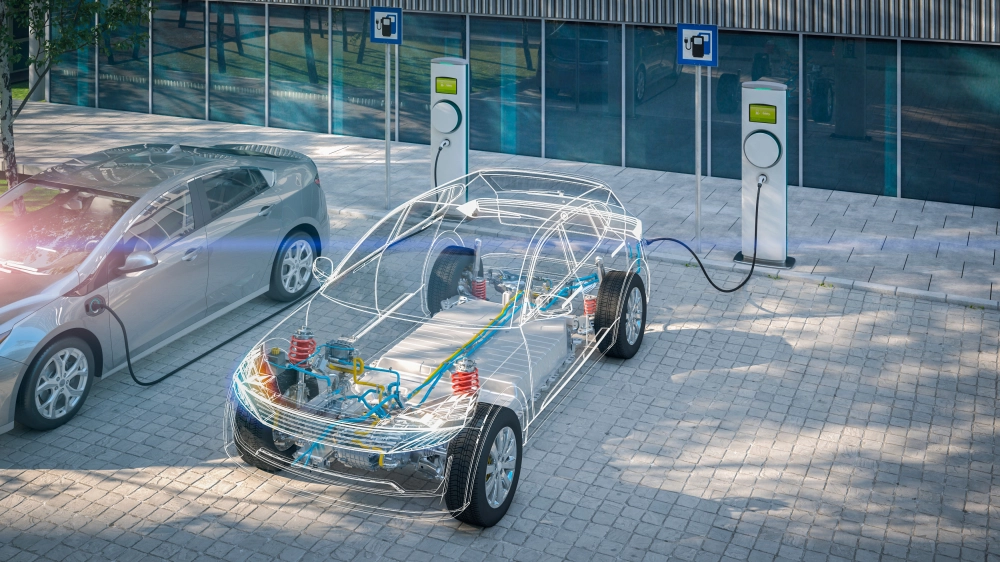
High Voltage Wire Harness Design
1. Dual Track Wire Harness Design
- As the operating voltage for high voltage wire harnesses in new energy vehicles is usually above 600V, a dual track design is employed to ensure safety. This means that the positive and negative circuits each use two separate conductors wrapped in insulation material. This guarantees that even if one conductor fails, it will not lead to an electric shock.
2. Selecting Materials for High Voltage Wire Harnesses
When selecting materials for high voltage wire harnesses, one should keep in mind the following factors:
- High Voltage Resistance: Materials must be able to withstand high voltage currents to prevent electric shock or breakdown.
- Heat Resistance: Materials should be heat resistant to prevent complications due to overheating during operation.
- Corrosion Resistance: Materials must be resistant to corrosion from acids, alkalis, salts, etc., during operation.
- Flame Retardancy: Materials must have flame retardant properties to prevent fires in the case of short circuiting or other complications.
Common materials used for high voltage wire harnesses include:
- Copper: Copper is commonly used due to its excellent conductivity and high voltage resistance.
- Aluminum: While aluminum is lighter than copper, it has lower conductivity. It is often used together with copper.
- Insulation Materials: Common insulation materials include PVC, PE, PP, XLPE, etc.
- Shielding Materials: Common shielding materials include copper mesh, aluminum mesh, braided mesh, etc.
3. Selecting High Voltage Connector Models
High-voltage connectors are critical components of a high voltage wire harness system. They are responsible for connecting and transmitting high voltages and high currents. When selecting a connector model, consider the following factors:
- High Voltage Resistance: Connectors should have high voltage resistance that stands up to the operating voltage of the wire harness.
- Protection Rating: Connectors should be suited for the environment they are used in, such as being waterproof and dustproof certified for outdoor use.
- High Voltage Interlock: High voltage interlock is a safety measure that prevents accidental electric shock during maintenance or operation.
- Shielding: Connectors should adopt shielding measures to reduce electromagnetic interference (EMI) with other electronic devices during use.
4. High Voltage Wire Harness Shielding Design
High voltage wire harnesses generate electromagnetic interference (EMI) when transmitting high voltage electricity. EMI can affect the normal operation of other electronic devices, even causing malfunctions. Therefore, shielding designs are necessary to help reduce EMI.
High voltage wire harness shielding designs mainly include the following two factors:
- Braided Mesh Wires: Braided shielding mesh can effectively absorb and reflect EMI, preventing it from radiating outwards.
- Connectors with Shielding Design: Connector shields can form a closed loop with the shielding mesh wires, further enhancing EMI suppression.
When collaborating with customers on high voltage wire harness requirements, CTE Tech considers EMI as a critical technical issue. Therefore, materials are selected with comprehensive shielding in mind to meet the quality requirements of our customers. CTE’s high voltage wire harness materials and processes comply with relevant regulations for electric vehicles, including ISO6722, ISO19642, QC/T 1037, GB/T 25085, LV216-1 and LV216-2 for wire materials; USCAR-2, and USCAR-37 for connector materials; USCAR-21, USCAR-37, and USCAR-38 for crimping technique; ISO6439-3 for high voltage testing; and ISO20653 for air tightness testing.