Electrical vehicle new era - High-Voltage Wiring Harness Layout Design
2024.07.03
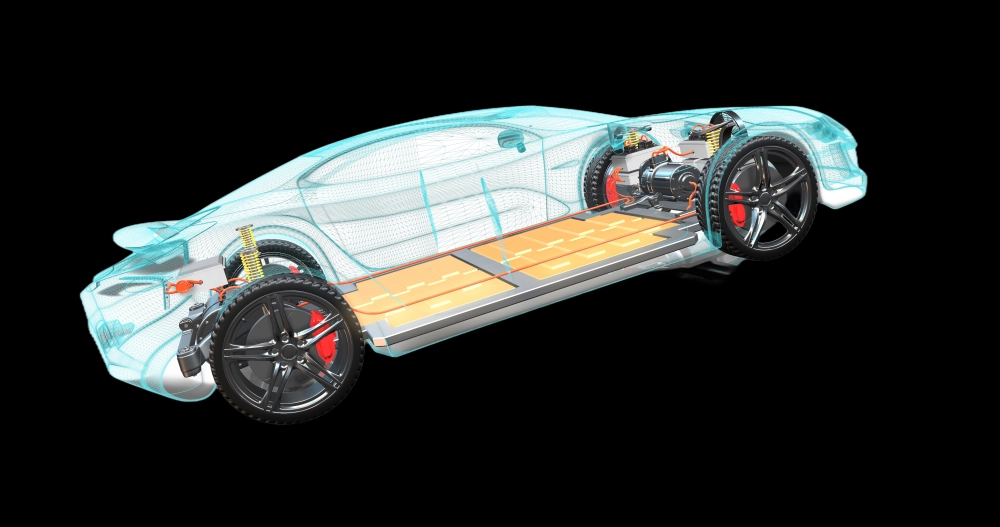
High-Voltage Wiring Harness Layout Design
The Importance of High-Voltage Wiring Harness Layout Design
The layout design of high-voltage wiring harnesses, critical to the development of new energy vehicles, requires careful consideration of a number of factors. The layout design of high-voltage wiring harnesses affects not only the performance and safety of the entire vehicle, but also production cost and maintainability.
Principles of High-Voltage Wiring Harness Layouts
1. Compact Layout
The longer a wiring harness, the greater the pressure drop and loss, leading to decreased motor efficiency and reduced battery life. Therefore, when installing a high-voltage wire harness, efforts should be made to shorten the length of the harness as much as possible. Factors such as harness length, cost, and installation difficulty should be considered carefully when selecting an appropriate layout design. For instance, for smaller new energy vehicles, a layered installation method can help save space; for larger new energy vehicles, a parallel installation method can improve layout efficiency.
2. Safe Layout
High-voltage wire harnesses should be hidden and comply with relevant collision safety regulations. In addition, effective protection measures should be taken for high-voltage wire harnesses to prevent electrical leakage, fires, and other potential hazards.
In practical application, the following measures can help ensure the safe layout of high-voltage wire harnesses:
- Arrange high-voltage wire harnesses inside the body of the vehicle to avoid exposure.
- Use appropriate protective materials, such as insulation sleeves, fireproof tape, etc., to protect the high-voltage wire harness.
With decades of experience in the production of automotive wiring harnesses, CTE Tech has a deep understanding and mastery of the wiring harness layout. Through cooperating on wiring harness layout with a number of domestic and foreign automotive manufacturers and car models, CTE develops the best wiring harness configuration for each project to meet the different layout requirements of each automotive wire harness.
Types of Layouts for High-Voltage Wiring Harnesses
1. Layered Layout
A layered layout refers to separating high-voltage and low-voltage wiring harnesses to avoid electromagnetic interference from high to low-voltage. The layered layout is currently the most commonly used layout method for high-voltage wiring harnesses. In practical application, this layout can be implemented in the following ways:
- Place the high and low-voltage wiring harnesses on different levels of the vehicle body, such as positioning the high-voltage harness at the bottom of the vehicle body and the low-voltage harness in the middle or upper part.
- Use metal shielding covers to separate the high and low-voltage harnesses.
Layered Layout example (photo courtesy via internet)
2. Parallel Layout
The parallel layout refers to arranging high and low-voltage harnesses along the same route while ensuring that they do not cross one another. Parallel layouts can save space but require a more technical installation.
Parallel Layout example (photo courtesy via internet)
Due to differences in vehicle structure, layout of electrical components, and limitations in layout space, both of the above layout forms can be seen in the average new energy vehicle’s wiring harness layout design. Combining different layout forms can minimize or neutralize interference between high and low-voltage wiring harness communication.
CTE Tech, in collaboration with clients, provides customized design and production to meet clients’ requirements for layout design. In recent years, CTE has acquired experience in producing high-voltage wiring harnesses for various types of electric vehicles, including mini electric vehicles, electric buses, and hybrid electric vehicles.
Safe Layout for High-Voltage Wiring Harnesses
1. Avoid Vibration Zones
High-voltage wiring harnesses should be kept away from areas with intense vibrations to prevent damage to the harness. Vibration can lead to fatigue damage, causing damage to the insulation layer at best and leading to harness breakage at worst, possibly resulting in safety issues such as electrical leakage and fire.
2. Avoid High-Temperature Zones
High temperatures can damage wiring harness insulation, resulting in electrical leakage at best and short circuits at worst, possibly leading to safety issues such as fire. Therefore, when installing wiring harnesses, it is important to avoid high-temperature vehicle components to prevent melting or accelerated aging, which could expose the core wires and cause short-circuiting with the vehicle frame. Common high-temperature components in new energy vehicles include air compressors, brake pipes, power steering pumps, and oil pipes, etc.
3. Bend Radius Design for High-Voltage Wires
The bend radius of high-voltage wiring harnesses should meet relevant standards to prevent problems such as increased resistance and damage to the insulation layer. During design and assembly, attention should be paid to the following:
- Avoid squeezing or vibrating the high-voltage wiring harness.
- High-voltage wiring harnesses exiting from the rear of high-voltage connectors should maintain a straight-line exit.
CTE Tech spares no effort in creating high-voltage wiring harnesses production lines that meet the usage and quality requirements of our automotive clients. We introduce state-of-the-art automatic equipment to reduce friction during wire feeding, improve wire cutting accuracy and operational efficiency, and minimize damage. High-precision semi-automatic equipment, such as shielding wire stripping machines, prevent damage to the shielding layer of high-voltage wiring harnesses during stripping, while professional cutting equipment for shielding layers can neatly cut high-voltage wiring harnesses without leaving behind debris.
4. Waterproof Sealing Design for High-Voltage Wires
To enhance the protection of high-voltage wiring harnesses, sealing measures such as sealing rings are used at connector locations to prevent the introduction of moisture and dust, ensuring a sealed environment and avoiding safety issues such as short circuits, sparks, and electrical leakage. To protect high-voltage wiring harnesses, orange temperature-resistant and flame-retardant coatings, such as corrugated pipes or fabric sleeves, are often used to prevent abrasion, reduce noise, provide heat insulation, and improve aesthetics.
CTE Tech utilizes high-precision composite automatic machines to complete the stripping process of high-voltage wires in one go. With the latest servo crimping machines, they ensure the best crimping quality. With the help of CTE-developed wiring assembly fixtures and assembly machines, they can complete difficult assembly tasks to meet the sealing, waterproofing, and other specifications required for high-voltage wires.