A Guide To Wire Harness Assembly Process
2024.08.14
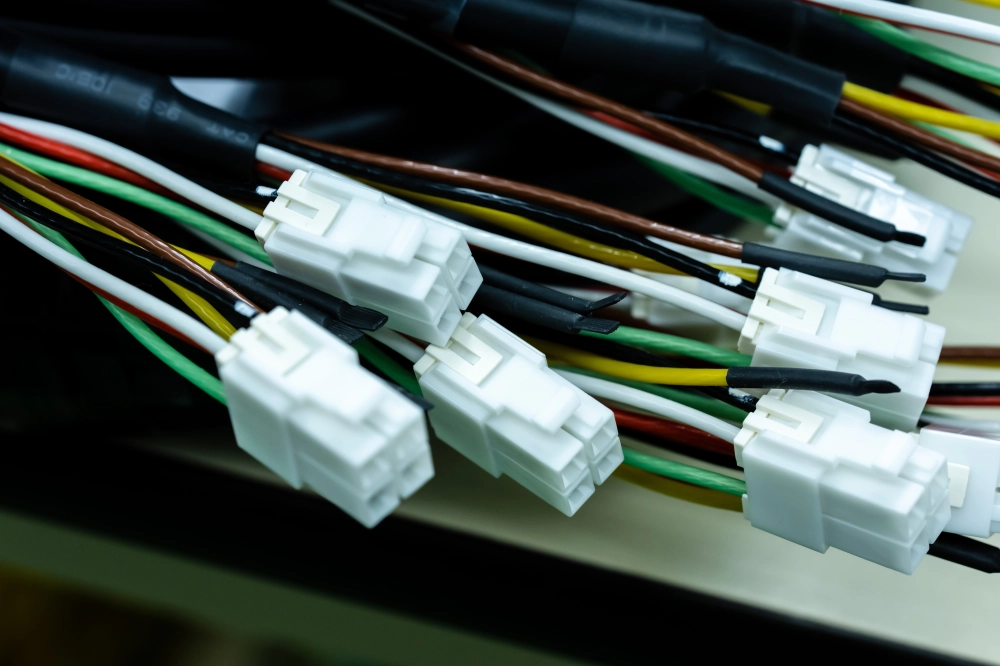
Wire harness assemblies are indispensable as the backbone of numerous electronic systems in the contemporary tech-intensive world. The Wire Harness Assembly Process, in all its intricate phases, caters to a range of industry applications, from consumer electronics to aerospace and automotive sectors. Being a meticulously structured bundle of wires, connectors, and terminals, these assemblies allow for the efficient transmission of electrical power and signals. Hence, they serve as the vital conduit in an array of complex devices.
Leveraging the advantages of these assemblies, including streamlined installations, improved reliability, and enhanced safety, industry professionals can foster a technologically powerful environment that promotes efficiency and mitigates the risk of error and potential harm.
As we go deeper into the wire harness assembly process, we shall explore its detailed steps from design and planning to final packaging. Plus, we shall discuss how industry leaders, like CTE Tech Corp., transform the sector through a commitment to quality assurance, provide competitive pricing, and deliver unparalleled customer service, which sets new benchmarks for operational excellence in the wire harness manufacturing process industry.
Wire Harness Manufacturing Process Step by Step
Design and Planning
The initial phase in wire harness manufacturing, design, and planning, is pivotal. It sets the foundation for the entire project. This step involves using Computer-Aided Design (CAD) software to create detailed blueprints and schematics. These plans ensure the wire harness will meet all the specifications required for its intended application. The accuracy of this stage is critical, as it dictates the functionality and integration of the wire harness into the final product, considering factors such as space constraints and electrical connectivity.
Material Selection
Choosing the right materials is crucial for the wire harness's performance and longevity. This step involves selecting suitable wires, connectors, terminals, and protective materials like conduits or looms. The selection is based on various factors, including the harness's operating environment, temperature ranges, electrical load requirements, and mechanical durability. This careful consideration ensures the harness will function reliably under expected conditions.
Wire Preparation
Wire preparation is a meticulous process that involves stripping the insulation from the wire ends and cutting the wires to specific lengths. This step is facilitated by high-precision machinery, which guarantees consistent results critical for the harness's functionality. The accuracy of wire preparation directly impacts the quality of terminal connections and the overall reliability of the wire harness.
Terminal Crimping
Terminal crimping attaches terminals or connector pins to the wire ends. This process is executed using a crimping machine, which applies the exact force needed to ensure a secure mechanical and electrical connection between the wire and terminal. The quality of the crimp is vital for the harness's electrical performance, requiring precise control over the crimping process.
Wire Rouitng and Bundling
During wire routing and bundling, wires are organized according to the design schematics and then grouped together. This organization is crucial for the harness to fit properly in its designated space and function as intended. Bundling is typically achieved using ties, wraps, or other securement methods, which protect the wires from damage and reduce the risk of electrical interference.
Connector Assembly
The connector assembly phase involves attaching the grouped wires to their corresponding connectors. This step requires precise attention to detail, as each wire must be inserted into the correct slot in the connector. The complexity of connectors can vary significantly, ranging from simple single-wire connectors to complex multi-wire configurations. Proper assembly is essential for the harness to function correctly.
Testing and Inspection
Testing and inspection are critical for ensuring the wire harness's reliability and safety. Electrical testing procedures check for issues such as short circuits, open circuits, and correct resistance levels. Additionally, visual inspections are conducted to verify the assembly's accuracy and detect any physical defects. These steps guarantee the harness meets the required quality standards.
Quality Control
Quality control is an overarching process that spans all stages of wire harness manufacturing. It includes continuous monitoring and regular audits to ensure each step meets high-quality standards. This comprehensive approach ensures the wire harness's reliability, durability, and compliance with relevant standards, thereby safeguarding the final product's performance.
Final Packaging
The final packaging step is crucial for protecting the completed wire harnesses during transportation. Careful packaging prevents physical damage and ensures the harnesses arrive in perfect condition. This phase often includes labeling and documentation, which facilitates tracking, inventory management, and installation, completing the wire harness manufacturing process with a focus on quality and customer satisfaction.
Wire Harness Manufactured by CTE
In conclusion, the wire harness assembly process demands precision, quality control, and expertise, all of which are encapsulated in the services offered by CTE Tech Corp. Their formidable presence in the wire harness manufacturing process is underlined by their unrivaled dedication to quality, displayed through a low defect rate (5 ppm).
Coupled with their competitive pricing, timely deliveries, and customer-centric services, they offer a comprehensive solution to all your wire harness requirements. By choosing CTE Tech Corp., you guarantee the quality and reliability of your products and streamline your operations, which allows your business to focus on its core competencies. So, why hold off? Just select CTE Tech Corp. as your wire harness manufacturer, and then allow yourself to enjoy the benefits of dealing with a dependable business partner.