What Is a Wire Harness and How Does It Work?
2024.08.14
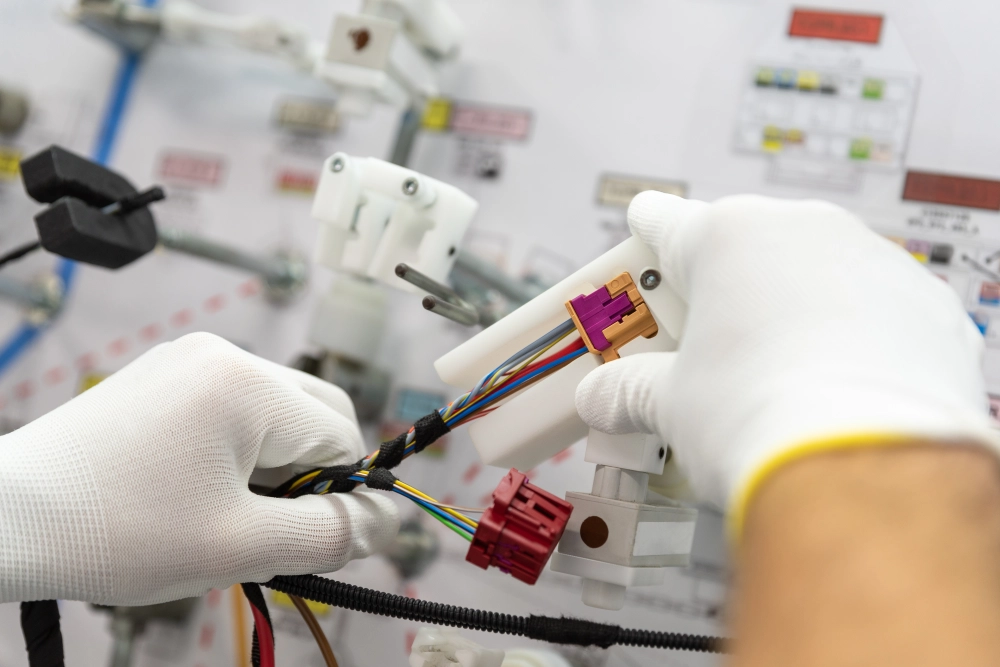
A wire harness is a crucial component that enables the proper functioning of electrical devices. The design and quality of the wire harness directly impact the flow of current and the overall success of any electrical system. In this article, we will explore what a wire harness is, how it works, its applications in various industries, and the process of designing and manufacturing high-quality wire harnesses. Let's dive in to discover the answers to these questions. Understanding the importance of wire harnesses and their role in electrical systems will help us appreciate the significance of their design and manufacturing processes. To begin our exploration, let's first understand the definition and functionality of a wire harness.
Wiring Harness Definition
A wire harness, also known as a wiring harness or cable harness, is a bundled arrangement of electrical wires, cables, and connectors that transmit electrical power and signals to various components and devices within a system. It serves as a central nervous system, providing a safe and organized means of interconnecting different electrical and electronic components.
Wire harnesses are designed to simplify the installation, maintenance, and troubleshooting processes in complex electrical systems. By bundling the wires and cables together, they minimize the risk of tangling, chafing, or interference between individual wires, ensuring a neat and organized layout. This not only improves the overall aesthetics but also enhances the system's reliability and performance.
One notable difference between a wire harness and a cable assembly is that a wire harness consists of multiple wires and cables bundled together, while a cable assembly usually refers to a single cable with connectors on both ends. This distinction often leads to confusion, as the terms are used interchangeably. However, the purpose of both wire harnesses and cable assemblies is to efficiently transmit electrical power and signals.
Where Is Wire Harness Used?
Wire harnesses find applications in various industries due to their versatility and effectiveness in solving electrical problems. Let's explore some key industries that utilize wire harnesses.
- Aerospace: Wire harnesses are essential in designing aerospace products such as drones, satellites, and aircraft, facilitating effective communication and interconnection.
- Medical industries: Hospitals rely on wire harnesses to protect and organize wires in medical equipment, enabling faster and more efficient treatment options for patients.
- Automotive industry: Wire harnesses are vital in the automotive industry, enabling space-saving integration within the dashboard and organizing complex wiring for easy identification and maintenance. They optimize space utilization as vehicles incorporate more electrical components, such as infotainment systems and ADAS. Wire harnesses simplify troubleshooting by grouping related wires and providing clear labeling. They also protect wires from damage, ensuring reliable and durable electrical systems. In summary, wire harnesses play a critical role in the success of vehicles by enhancing efficiency, reliability, and ease of maintenance in the automotive electrical infrastructure.
- Robotics: Wire harnesses are used in robotics and automated equipment to organize and safeguard wiring, allowing for seamless functioning. They also find applications in computers, laptops, and servers, optimizing space and facilitating easy identification of wires.
- Manufacturing industry: Wire harnesses are employed in manufacturing processes for routing and organizing wiring. They are also utilized in the construction sector for efficient wiring insulation.
How Is a Wire Harness Designed and Manufactured?
The design and manufacturing process of wire harnesses involves multiple stages. It begins with the design team creating precise measurements based on project specifications using computer programs. Prototypes are then produced and extensively tested for functionality, durability, and safety.
Any logistical issues, such as wire routing or interference, are addressed at this stage. After finalizing the design and prototype testing, production begins, involving careful selection and routing of wires, integration of connectors and terminals, and securing them with protective sleeves or looms. Automated equipment ensures consistent quality. Thorough testing is conducted to verify electrical integrity, and visual inspections are performed before distribution.
What Is Meant by Wire Harness Design?
Wire harness design refers to the process by which an engineer examines the needs of an electrical component of a system, taking into account the physical space available, and then creating an assembly of wires that will be used to transfer power and data.
For instance, an airplane's wiring harness must supply power to everything on the airplane—from the landing gear to passenger comforts and flight controls. The design must account for passenger and crew comfort, weight distribution, and other vital factors to ensure safe and smooth transport.
To deepen your understanding of the intricacies in wire harness design and manufacturing, explore 'Cable and Harness Assembly: Exploring the Distinctions'. This post delves into the key differences and specific applications of wire harnesses and cable assemblies, enhancing your knowledge in this critical field.
Challenges in Creating Wiring Harnesses
Creating wiring harnesses poses several challenges in the manufacturing process. Let's take a look at some of the major challenges:
- Data inconsistency: Sharing consistent data across teams and locations can be difficult, leading to delays in vehicle launch.
- Limited reuse: Challenges arise in reusing designs that do not match, requiring new designs or significant modifications.
- Manufacturing complexity: Highly intricate assembly procedures and strict quality standards contribute to the complexity of harness production.
- Time to market pressures: Meeting deadlines while ensuring design requirements and quality standards can be challenging.
Benefits of Wire Harnesses
There are many benefits to using wire harnesses for wiring applications, including:
- Simplified Installation: Wire harnesses provide a streamlined and organized approach to wiring installations. By bundling multiple wires and cables together, they eliminate the need for individual wire routing and separate connections. This simplifies the installation process, reduces the chances of errors, and saves valuable time during system assembly.
- Enhanced Reliability: The precise design and manufacturing of wire harnesses ensure reliable and consistent electrical connections. The secure bundling of wires minimizes the risk of loose connections, short circuits, or wire damage due to environmental factors. This reliability translates to improved system performance, reduced downtime, and enhanced overall durability.
- Improved Safety: Wire harnesses are designed with safety in mind. They incorporate features such as insulation, shielding, and protective sleeves to prevent electrical hazards. By properly routing and securing the wires, wire harnesses reduce the risk of accidental contact, electrical interference, or fire hazards, making them a safer solution for electrical systems.
- Easy Maintenance and Troubleshooting: The organized and labeled nature of wire harnesses simplifies maintenance and troubleshooting processes. With wires neatly bundled and labeled, technicians can easily identify and access specific components, making repairs or replacements more efficient. This reduces downtime, enhances system uptime, and minimizes overall maintenance costs.
- Customizable and Scalable: Wire harnesses can be tailored to meet specific system requirements. Manufacturers can customize the harness design, including the length, color coding, and connectors, to match the unique needs of the application. Moreover, wire harnesses are scalable, allowing for easy expansion or modification of electrical systems as requirements change or new components are added.
- Improved Signal Integrity: In systems where signal integrity is crucial, such as high-speed data transmission or sensitive electronic devices, wire harnesses play a vital role. They are designed to minimize electromagnetic interference (EMI) and crosstalk, ensuring that signals remain clean and undistorted, resulting in reliable data transmission and optimal performance.
- Cost Efficiency: While wire harnesses may require upfront investment in design and manufacturing, they offer long-term cost benefits. By reducing installation time, minimizing the risk of errors or rework, and enhancing system reliability, wire harnesses contribute to overall cost savings throughout the lifecycle of the electrical system.
Wire Harness Solutions - CTE
Wire harnesses play a vital role in modern electrical systems, providing a reliable and efficient means of interconnecting components. Understanding the design and manufacturing process of wire harnesses, as well as the challenges faced by manufacturers, highlights the complexity and importance of this technology.
Despite the challenges, wire harnesses offer substantial benefits, including cost reduction, enhanced organization, reduced installation time, protection of conductors, improved work environment, increased safety, and decreased installation and maintenance time. These advantages make wire harnesses a preferred choice for a wide range of industries and applications.
At CTE, we specialize in designing and manufacturing high-quality wire harnesses tailored to meet your specific needs for custom wire harness solutions. With our expertise, cutting-edge technology, and commitment to customer satisfaction, we deliver reliable and efficient wire harness solutions that exceed expectations. Contact us today to discuss your wire harness requirements and discover the CTE difference.