Unveiling the Hazards: Exploring the Main Risks in Electric Vehicle Repair
2024.08.14
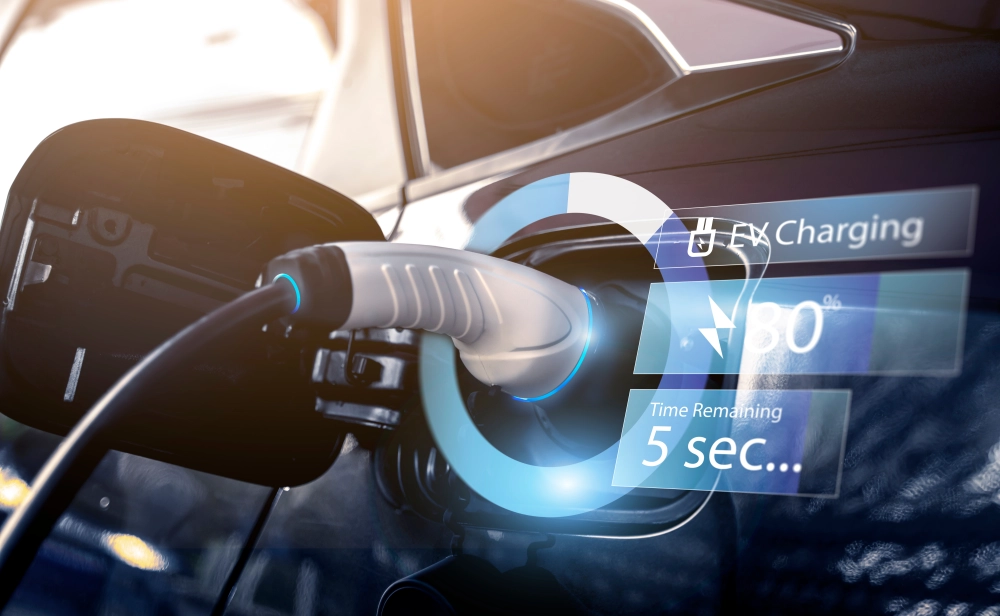
Hybrid and electric vehicles (HVs) have revolutionized the automotive industry, offering sustainable and energy-efficient transportation solutions. However, these innovative vehicles bring new challenges and risks to the workplace, requiring additional precautions beyond those typically associated with vehicle repair and maintenance. In this blog post, we will explore the unique hazards presented by E&HVs and discuss the importance of additional skills and training for technicians to ensure the safe handling of electric and hybrid vehicles.
Types of E&HVs
When it comes to electric and hybrid vehicles (E&HVs), there are three distinct types that each offer unique characteristics and capabilities. In this section, we will delve deeper into these vehicle types to provide a comprehensive understanding.
- Battery electric vehicles (BEVs): This type of E&HV operates solely on electric power, utilizing a large-capacity battery and an electric motor to propel the vehicle. Instead of relying on traditional fuels, BEVs require regular charging of the battery to maintain their functionality. This can be conveniently done by connecting the vehicle to an electrical supply network. Notably, BEVs possess the capability to recover and store energy during braking, contributing to increased efficiency and extended driving range.
- Hybrid electric vehicles (HEVs): HEVs combine two primary sources of energy for propulsion: an internal combustion engine (powered by petrol or diesel) and a battery. The advantage of an HEV lies in its ability to automatically select the most suitable energy source while in motion, and it can even utilize both simultaneously when required. The battery in an HEV can be charged through the internal combustion engine, and energy can also be recovered from the braking system, optimizing overall efficiency.
- Plug-in hybrid electric vehicles (PHEVs): Similar to HEVs, PHEVs also incorporate an internal combustion engine and a battery as energy sources. However, PHEVs possess an additional advantage over their counterparts, as they can be charged directly from an electric supply network. This means that in addition to utilizing the internal combustion engine and recovering energy during braking, PHEVs can also leverage the convenience of electric charging, further enhancing their sustainability and versatility.
By understanding the distinctions between these E&HV types, technicians can effectively address their specific requirements during repair and maintenance tasks. It is crucial for technicians to acquire specialized knowledge and training to navigate the intricacies of these vehicles and ensure the safe handling and operation of electric and hybrid vehicles in the workplace.
The Main Risks in Electric Vehicle Repair Include:
Hybrid and electric vehicles (HVs) bring additional hazards to the workplace beyond those typically associated with vehicle repair and maintenance. These risks include:
- Presence of high voltage components and cables that have the potential to deliver a fatal electric shock.
- Storage of electrical energy that poses a risk of explosion or fire.
- Components that can retain a dangerous voltage even when vehicles are switched off.
- Possibility of unexpected movement of electric motors or the vehicle itself due to magnetic forces within the vehicle and its systems.
- Heavy, bulky, and challenging to handle components, particularly high-voltage batteries that are significantly heavier than conventional batteries. Lifting aids and devices are necessary to prevent musculoskeletal disorders.
- The potential release of explosive gases and harmful liquids if batteries are damaged, overcharged, or improperly modified.
- Electric vehicles operate silently, increasing the risk of people being unaware of planned or unexpected movements.
- Hybrid vehicles automatically start their internal combustion engine when the ignition is on and the battery requires recharging.
Top Tips for Working Safely With E&HVs
To work safely with electric and hybrid vehicles (E&HVs), it is essential for professionals in the auto or vehicle repair industry to acquire additional skills and training. Here are some examples of how to handle E&HVs safely:
- Use appropriate personal protective equipment (PPE), such as insulated gloves, when working with high-voltage systems.
- Familiarize yourself with the location of high-voltage cables and components to avoid accidental contact.
- Follow the manufacturer's guidelines and safety procedures for handling E&HVs.
- Ensure proper training in handling high-voltage systems, including understanding the electrical architecture of E&HVs.
- Perform a thorough inspection of the vehicle's electrical system before initiating any repairs or maintenance work.
- Disconnect the vehicle's power source and isolate the high-voltage system before working on E&HVs.
- Adhere to lockout/tagout procedures to prevent unexpected energization of the vehicle's electrical system.
- Stay updated on the latest technologies, safety standards, and best practices related to E&HVs through continuous education and training.
- Have access to relevant service manuals, diagnostic tools, and equipment specifically designed for E&HVs.
- Maintain a clean and organized workspace to minimize the risk of accidents and ensure proper handling of E&HVs.
By following these guidelines and continually enhancing their knowledge and skills, professionals in the auto or vehicle repair industry can effectively and safely handle electric and hybrid vehicles.
To further understand the importance of these safety practices within the broader context of the automobile industry, delve into 'The Impact and Integration of Electric Vehicle Safety Standards in the Automobile Industry'. This article offers a comprehensive view of how safety standards are shaping the production and reliability of electric vehicles, providing essential insights for professionals in the auto repair industry.
The Role of Wire Harness Design and Manufacturing in Ensuring Safe E&HV Operation
Wire harness designers and manufacturers play a critical role in ensuring the safe operation of electric and hybrid vehicles (E&HVs). By understanding the unique risks involved in working with E&HVs and implementing appropriate measures, they can contribute to the overall safety and success of these advanced automotive technologies.
Designing for Safety
Wire harness designers must prioritize safety in their designs for E&HVs. This includes incorporating insulation, protective covers, and secure routing to minimize the risk of electrical shock or short circuits. Attention should also be given to the weight and size of high-voltage components, ensuring proper support and strain relief to prevent accidents caused by loose or damaged connections. By designing wire harnesses with safety as a central focus, designers can help mitigate risks and ensure reliable power distribution throughout the vehicle.
Manufacturing Quality and Compliance
Manufacturers of wire harnesses for E&HVs must establish stringent quality control processes. Thorough testing of the harnesses' electrical insulation, voltage resistance, and compatibility with vehicle systems is essential to guarantee their integrity and safety. Adherence to industry standards and regulations is paramount, as it ensures that wire harnesses meet the necessary safety requirements and are reliable in demanding E&HV environments.
Collaboration for Safety
Collaboration and communication between wire harness designers, manufacturers, and repair technicians are vital to ensuring the seamless integration and safe operation of electrical systems in E&HVs. Sharing knowledge and expertise can lead to the development of more efficient and reliable wire harnesses that mitigate risks and meet the evolving demands of the electric and hybrid vehicle market. By fostering strong partnerships throughout the industry, wire harness designers and manufacturers can contribute to the overall safety of E&HVs.
Final Thoughts
Wire harness designers and manufacturers have a crucial role to play in ensuring the safe operation of electric and hybrid vehicles (E&HVs). CTE Tech Corp., a leader in the field, is committed to building trust by delivering innovative solutions for the vehicle business. Their focus on quality, agility, and cost efficiency is evident in their offerings:
- Quality Assurance: CTE provides high-quality products, including high-voltage and low-voltage wiring harnesses suitable for electric vehicles. Their focus on customer-centered production and adherence to global manufacturing standards ensures top-notch quality assurance.
- Dynamic Solutions: Through continuous improvement in ordering and manufacturing information operations, CTE optimizes manufacturing workflows, boosting production efficiency, and quickly addressing customer needs.
- Diverse Applications: CTE offers professional wire harness services for various vehicles, including automobiles, motorcycles, ATVs, buses, trains, construction machinery, agricultural machines, and more.
- Future Innovations: CTE is passionate about innovating and developing new functionalities for the future of automotive mobility, positioning itself as a reliable supply chain partner in key automotive components.
By prioritizing safety in their designs, manufacturing processes, and collaborations with repair technicians, CTE contributes to the overall safety and success of E&HVs. Through continuous improvement, adherence to standards, and effective communication, CTE, along with the broader wire harness industry, can help pave the way for a cleaner and more sustainable future of transportation.