Understanding Electrical Wire Harness Design and Production
2024.08.14
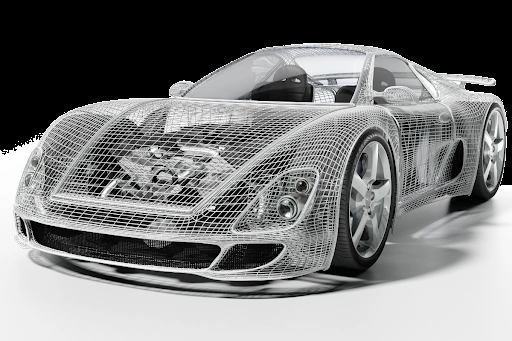
CTE Tech Corp. understands that electrical wire harness design and production are crucial components of any electronic device. A wire harness, as we define it, is an assembly of wires, cables, and connectors used to route power and signals between electronic components. When it comes to the design of electrical harnesses, we consider many factors. We are fully aware of the design process, as well as the different types of connectors and components that can be used in the production of electrical harnesses.
Electrical harness design and production is a critical aspect of the manufacturing process for various devices and systems, particularly in the automotive and electronics industries. Suffice it to say, having a good grasp of the intricacies involved in the entire process, from material selection to assembly techniques, can lead to the optimal flow and reliability of electrical currents.
Key Considerations in Wire Harness Design
At CTE Tech Corp., we pay attention to several considerations that can significantly impact the performance of a wire harness. For instance, during the electrical harness design process, we focus on the following key aspects:
- Environmental conditions: Consider factors such as temperature, humidity, vibration, and exposure to chemicals or moisture. All of these can affect the power and durability of the wire harness.
- Wire specifications: Determine the appropriate wire length and thickness (gauge) based on the power requirements, voltage drop, and signal quality. This ensures efficient power transmission and minimal signal loss.
- Insulation: Choose the right insulation material to protect the wires from environmental factors, as well as to provide electrical isolation and prevent short circuits.
- Connector types: Select the appropriate connectors that are compatible with the devices being connected, ensuring proper signal transmission and secure connections.
- Routing: Plan the cable harness design to minimize electromagnetic interference, optimize space utilization, and facilitate ease of installation and maintenance.
- Safety and compliance: Ensure that the cable harness design follows the necessary industry standards, regulations, and safety requirements, such as UL, CSA, or RoHS. This helps maintain high safety levels for both end-users and the environment.
- Strain relief: Integrate strain relief solutions, like cable clamps or grommets to protect the wires and connectors against mechanical stress due to bending, twisting, or pulling forces.
- Serviceability: Create the wire harness focusing on easy maintenance and repair. This could involve utilizing modular connectors, color-coding wires, or adding service loops to streamline troubleshooting and component replacement.
- Electromagnetic compatibility (EMC): Examine the likelihood of electromagnetic interference (EMI) between the wire harness and other system components. Apply shielding methods, such as using shielded cables or ferrite beads, to decrease EMI and ensure accurate signal transmission.
- Cost-effectiveness: Keep in mind the total cost, including material costs, assembly time, and maintenance expenses, when designing the wire harness. Refine the design to balance performance and cost, while still satisfying the application requirements.
- By paying attention to these things, designers can further enhance the reliability of the wire harness, thus, creating a product that is not only efficient and effective but is also safe, durable, and cost-effective.
What Is a Wire Harness Diagram and Why Is It Crucial?
A wire harness diagram is another crucial component in the electrical harness design process, as it provides a clear and concise visual representation of the wiring configuration within a system. This diagram outlines the specific connections, wire routing, and component locations, ensuring that the production and assembly processes are efficient and accurate.
Needless to say, a wire harness diagram ensures that all connections are made correctly, wires are routed most effectively, and potential issues can be easily identified and resolved during the troubleshooting process.
What Do You Need to Design a Cable Harness?
Designing an electrical cable harness requires a wide array of components and materials. This includes the following:
- Wire Strippers - Wire strippers are used to remove the insulation from the wires, exposing the conductive material underneath. This is important for creating proper connections between wires and connectors.
- Crimping Pliers/Ratcheting Crimpers - Crimping pliers or ratcheting crimpers are used to secure connectors onto the ends of wires, ensuring a strong and reliable connection.
- Wires/Cables - You'll need a variety of wires and cables in different sizes, colors, and materials, depending on the specific requirements of your cable harness. Make sure to choose the right type of wire for your project, considering factors like voltage, current, and environmental conditions.
- Cable Ties/Zip Ties - Cable ties or zip ties are used to bundle and organize wires within the harness, making it neat and easy to manage. These ties come in various sizes and materials, so choose the ones that best suit your needs.
In addition to these basic tools and materials, you may also need other items like connectors, heat shrink tubing, cable sleeves, and labels to design a complete and professional cable harness.
Steps in Wire Harness Design and Production
Wire harness design and production involve creating an organized layout for multiple wires and cables, resulting in a unified harness that ensures optimal performance and functionality. With careful consideration of factors such as wire length, gauge, insulation, and connector types, the design phase sets the foundation for a successful wire harness. The steps involved in electrical harness design and production include:
- Design: This initial stage involves determining the specific requirements of the wire harness, such as wire types, connector types, and layout. It also includes creating a detailed wire harness diagram that serves as a blueprint for the entire project.
- Prototyping: Once the design is finalized, a prototype is created to test the functionality and fit of the wire harness. This step allows for any necessary adjustments and improvements to be made before moving on to full-scale production.
- Production and Assembly: In this stage, the wire harness is produced and assembled, with a strong focus on management to ensure efficiency, accuracy, and quality control. This may involve tasks such as cutting wires to the correct lengths, stripping insulation, crimping connectors, and bundling wires using cable ties or other organizational methods.
- Testing: After the wire harness has been produced and assembled, it undergoes rigorous testing to ensure proper functionality, safety, and performance. This may include tests for continuity, insulation resistance, and voltage. Any issues identified during testing are addressed and corrected before the wire harness is deemed ready for use.
For more insights on what is a wire harness and how it works, refer to our previous post.
Choosing the Right Cable Harness Design Partner for Your Project
When it comes to cable harness design and production, partnering with the right company can make all the difference in the success of your project. Choosing a cable harness design partner with strong management capabilities and a proven track record of reliability is crucial to ensuring the timely delivery and consistent quality of your wire harnesses.
CTE stands as a frontrunner in the cable harness design industry, placing a strong emphasis on management and reliability. Our expertise in these areas has led to a 100% delivery rate, ensuring that our clients consistently receive their wire harnesses on schedule. Moreover, our dedication to maintaining stable inventory levels signifies that you can rely on us to have the necessary materials and components readily available when needed.
By choosing to collaborate with a trusted industry leader, you can confidently move forward with your cable harness design and production endeavors.